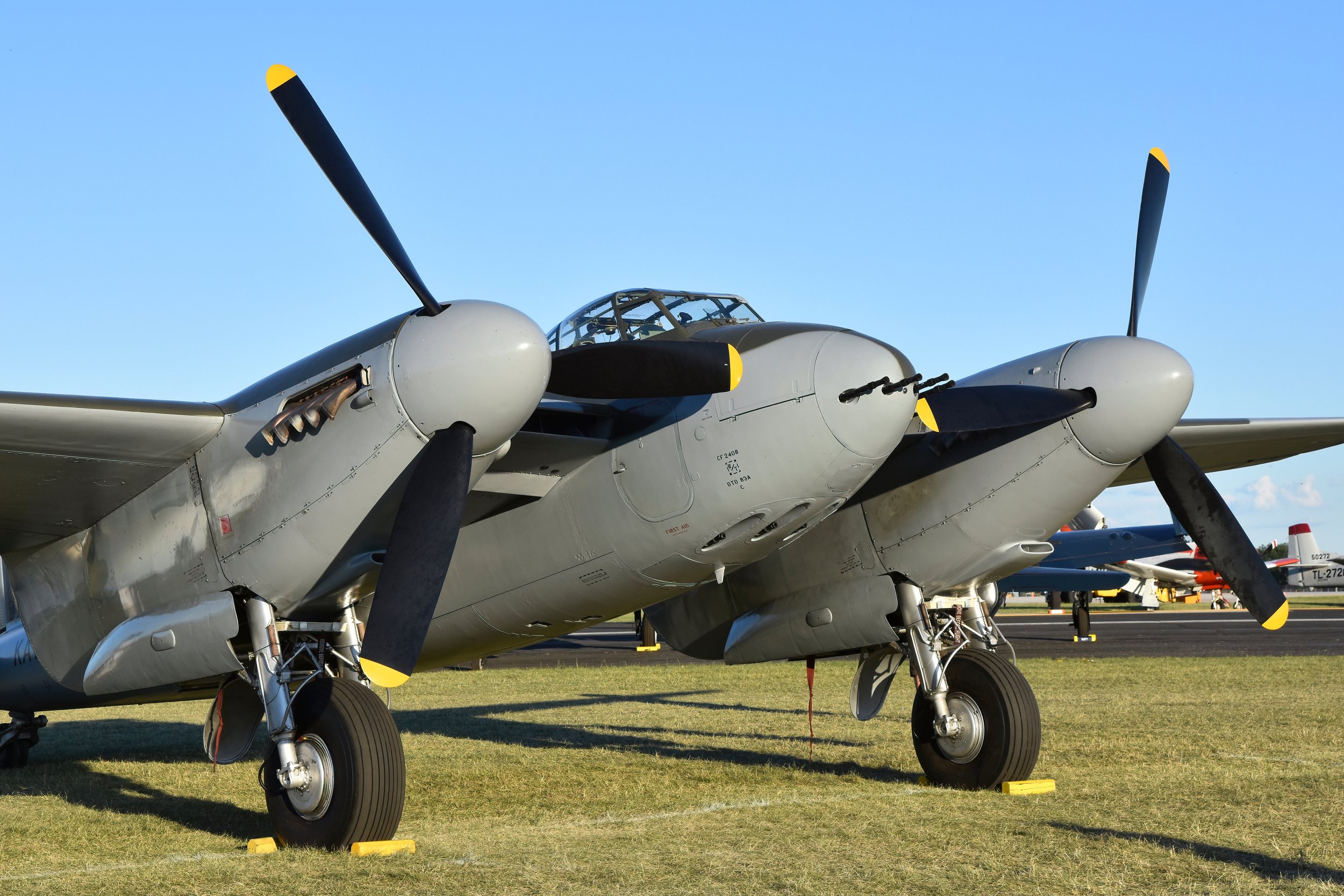
November 25 / De Havilland Mosquito first flight
First Flight 25 November 1940
De Havilland Mosquito
The de Havilland DH.98 Mosquito, a remarkable British twin-engined, multirole combat aircraft, emerged as one of the most innovative and versatile aircraft during the Second World War. Its introduction marked a significant departure from conventional aircraft design, primarily due to its predominantly wooden construction. This unique feature earned it the affectionate nickname “Wooden Wonder” or “Mossie” among its admirers. The Mosquito’s journey from conception to operational deployment is a fascinating tale of innovation, perseverance, and strategic foresight.
The Mosquito’s story begins with its unconventional design philosophy, championed by Geoffrey de Havilland and staunchly defended by Air Chief Marshal Sir Wilfrid Freeman. The aircraft was initially conceived as an unarmed fast bomber, a radical departure from the heavily armed and armored bombers of the time. This design choice was met with skepticism and was even dubbed “Freeman’s Folly” by Lord Beaverbrook, the Minister of Aircraft Production. However, Freeman’s unwavering support ensured the project continued despite calls to abandon it. When the Mosquito first took to the skies in 1941, it quickly established itself as one of the fastest operational aircraft in the world, a testament to the visionary design and engineering prowess of its creators.
The Mosquito’s versatility became its hallmark as it evolved to fulfill a wide array of roles throughout the war. Initially designed as a fast bomber, it soon adapted to serve as a low- to medium-altitude daytime tactical bomber, a high-altitude night bomber, a pathfinder, a day or night fighter, a fighter-bomber, an intruder, a maritime strike aircraft, and even a photo-reconnaissance platform. Its adaptability extended beyond combat roles; the British Overseas Airways Corporation utilized it as a fast transport aircraft, ferrying small, high-value cargo through enemy-controlled airspace to and from neutral countries. The Mosquito’s two-man crew, comprising a pilot and a navigator, sat side by side, and in emergencies, a single passenger could be accommodated in the bomb bay.
Perhaps one of the most celebrated versions of the Mosquito was the FB Mk. VI, which was frequently deployed in special operations. Notable among these was Operation Jericho, a daring raid on Amiens Prison in early 1944. The aircraft’s precision and speed were also demonstrated on 30 January 1943, during a raid on Berlin that knocked out the main broadcasting station, cutting off a speech by Hermann Göring on the 10th anniversary of Hitler’s ascension to power.
The Mosquito’s operational reach extended across various theaters of war. It flew with the Royal Air Force (RAF) and other allied air forces in the European, Mediterranean, and Italian theaters. It also saw action in the Southeast Asian theater and was operated by the Royal Australian Air Force in the Halmaheras and Borneo during the Pacific War. By the 1950s, the RAF began replacing the Mosquito with the jet-powered English Electric Canberra, marking the end of an era for this iconic aircraft.
The Mosquito’s development was rooted in de Havilland’s earlier successes with high-speed aircraft, such as the DH.88 Comet racer and the DH.91 Albatross airliner. The latter’s composite wood construction principles were adapted for the Mosquito, allowing it to achieve remarkable speed and agility. The aircraft’s wooden monocoque construction not only reduced weight but also simplified production, making it a practical choice during wartime shortages of strategic materials like aluminum and steel.
The British Air Ministry’s Specification P.13/36, issued in 1936, called for a twin-engined medium bomber with specific performance criteria. While many aviation firms proposed heavy designs with advanced engines and defensive turrets, Geoffrey de Havilland envisioned a different approach. Drawing on his experience with the Albatross, he believed that a bomber with an aerodynamic design and minimal skin area could exceed the performance requirements. His vision was to create a fast, wooden aircraft that relied on speed and maneuverability rather than armament for defense.
Despite initial skepticism from the Air Ministry, de Havilland’s persistence paid off. The Mosquito’s design evolved, and by September 1939, preliminary estimates for various configurations were produced. The outbreak of war in 1939 made the Air Ministry more receptive to the Mosquito’s potential, although there were still reservations about its unarmed design. However, the project’s momentum continued, and in 1940, the Mosquito was officially named and production plans were authorized.
The Mosquito’s construction was innovative for its time. The fuselage was a frameless monocoque shell made of plywood-balsa-plywood sandwich, providing excellent strength and stiffness. The wings were a single structural unit with continuous spars running from wingtip to wingtip. This design minimized weight while maximizing aerodynamic efficiency. The aircraft’s systems were equally advanced, with features like pressurized fuel tanks and electric-pneumatic radiator shutters.
The Mosquito’s operational history is a testament to its effectiveness and adaptability. It was involved in numerous special operations and precision strikes, showcasing its ability to penetrate enemy defenses and deliver devastating blows. Its speed and agility allowed it to outmaneuver enemy fighters and evade anti-aircraft fire, making it a formidable asset in the Allied arsenal.
Despite its wooden construction, the Mosquito proved to be a durable and reliable aircraft. However, it did face challenges in certain environments, such as the Far East, where extreme conditions led to concerns about structural integrity. Investigations revealed construction defects, but these were addressed, and the Mosquito continued to perform admirably in various theaters of war.
In summary, the de Havilland DH.98 Mosquito was a groundbreaking aircraft that defied conventional design principles. Its wooden construction, speed, and versatility made it a vital asset during World War II, and its legacy endures as a symbol of innovation and adaptability in military aviation history.
Mosquito Facts
Wooden Construction: The Mosquito was primarily constructed from wood, earning it the nickname “Wooden Wonder.” This design choice was made to conserve strategic materials like aluminum and steel during wartime shortages.
Versatility: Initially conceived as an unarmed fast bomber, the Mosquito evolved to perform a variety of roles, including tactical bomber, night fighter, photo-reconnaissance aircraft, and maritime strike aircraft.
Speed: In 1941, the Mosquito was one of the fastest operational aircraft in the world, capable of outrunning many contemporary fighter planes.
Minimal Crew: The aircraft was designed to operate with a minimal crew of two— a pilot and a navigator—sitting side by side, unlike the larger crews required for other bombers of the time.
Special Operations: The Mosquito was frequently used in special operations, such as Operation Jericho, a raid on Amiens Prison, and precision strikes on Gestapo headquarters.
Global Service: It served in various theaters during World War II, including Europe, the Mediterranean, Southeast Asia, and the Pacific, with the Royal Air Force and several other Allied air forces.
Innovative Design: The Mosquito’s design featured a frameless monocoque fuselage and a single structural wing unit, which contributed to its light weight and high performance.
Photo-Reconnaissance: The Mosquito was highly effective as a photo-reconnaissance aircraft, providing valuable intelligence due to its ability to fly fast and high, often avoiding enemy defenses.
American Interest: Although the United States did not pursue licensed production of the Mosquito, the USAAF evaluated the design, recognizing its impressive performance.
Legacy: Despite being replaced by jet-powered aircraft like the English Electric Canberra in the 1950s, the Mosquito remains a celebrated example of innovative aircraft design and versatility in military aviation history.